As South Africa's industrial sectors mature, facilities inevitably come to the end of their useful life. While the mining sector is accustomed to plan and provide for closure, much of the rest of the industrial sectors frequently underestimate the cost and challenges involved.
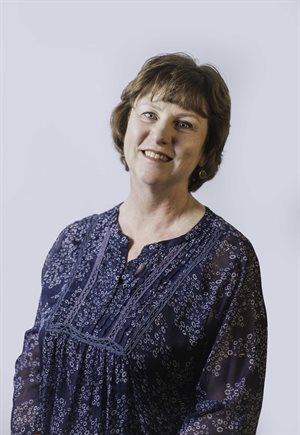
Heidi Snyman, technical director: contaminated land management, WSP in Africa
Many industrial organisations focus their closure planning and concurrent contaminated land rehabilitation planning towards ensuring they have the financial means to implement the conditions of environmental authorisations, and towards limiting or reducing adverse effects on the receiving environment.
The assumption is often that the infrastructure will remain in use, though by another owner or operator. This leads to underestimation of the financial provisioning that needs to be made for the full decommissioning and remediation, and planning is left until closure is imminent. Lessons can be learnt from global and listed companies in which shareholder reporting requirements demand robust planning and provisioning for closure.
The first lesson is to plan well ahead. Decommissioning, closure, and aftercare costs are often notably higher than expected when planning is done too close to the closure date and a simplistic closure scenario is assumed. Closure liabilities are also often under-represented until the last few years before closure, and a large increase in closure costs is often seen in the last few years of the facility’s operational life.
Planning further ahead
Since this is when cash flows and profits from continuing operations are rapidly decreasing, unexpected cost hikes lead to a focus on decreasing costs without adequately considering the risks of these decisions. By planning further ahead, industrial organisations can account for associated costs and liabilities more adequately.
The second lesson is that closure costs should be realistic and defensible, and realistic closure scenarios must be based on the next intended land use. Industrial operators should consider questions such as: What is the closure vision and what will the land be used for after closure? Will other operators continue to use the facilities or not? If not, what needs to be done with regards to transfer and repurposing? Is a change of land zoning needed? Will partial or full demolition form part of our closure activities? And if yes, will construction be needed before we can hand over?
Multi-disciplinary effort
Closure planning is an integrated process that should start as early as possible. The plan should be critically assessed regularly to accommodate changes in expectations. It should also be a multi-disciplinary effort that includes representatives with expertise in environment and rehabilitation, finance, legal, engineering and technical services, social impact and the affected community, and health and safety to avoid conflict in the closure decision-making processes.
When planning for closure with the end in mind, site investigations are critical. Social aspects must also be considered as large parts of the local community may be affected. Large industrial operations may be one of only a small handful of employers in the region, for example. This makes communication with stakeholders and partners, as well as public participation, vitally important during the planning and closure process.
The next step is to identify the environmental-related authorisations required, including the process and duration, to commence with the demolition and related activities. This will include an assessment of the requirements in terms of a variety of acts and associated regulations.
Meeting a range of priorities
For industrial operations to retire their assets responsibly, closures must be thoroughly planned in advance and adequate financial provision made for the retirement of industrial assets. The importance of planning and execution to meet a range of priorities for different roleplayers and stakeholders cannot be understated. Neither can the importance of adaptive management.