The implementation of Stage 6 load shedding scares all of us, but it may also put automotive parts suppliers - the lifeblood of South Africa's advanced car industry - out of business. The South African heavy industry has been forced to innovate by necessity. When your power demands are huge, Eskom's inability to fulfil its mandate triggers anxiety... and action.
With global orders to fulfil, South African automotive assembly facilities have not been indifferent to the off-grid concept. Impressive solar installations and all manner of clever alternative power sources, independent of the stumbling reality of Eskom, have been integrated by the country’s local vehicle manufacturers.
Take a broad view of the South African automotive industry, and the power risk doesn’t look too terrible. Automotive assembly, unlike food retail, doesn’t require a demanding cold chain refrigeration commitment. The paint shop’s chemical stability and curing lights are probably your most sensitive power-off risk.
But beyond industry conferencing optimism and thought leaders drinking glasses half full of Kool-Aid, the developing risk to localised automotive assembly is massive. And on the increase.
An issue outside the factory gates

East London has been deindustrialising for years, with Mercedes-Benz’s factory the only notable exception. But its solar power generation can’t support everyone.
To understand why Eskom’s escalations to and beyond stage 6 could tip the entire automotive assembly industry into crisis, think beyond Rosslyn, Prospecton, Silverton, Kariega, Gqeberha and the Buffalo River. BMW, Nissan, Toyota, Ford, Volkswagen (VW), Isuzu, and Mercedes-Benz’s core assembly assets have secure power, the result of engineers and management recognising that Eskom was beyond repair a decade ago.
But the issue is not at the final assembly stage. It’s in the supplier community. Those small engineering shops and enterprises supply the diversity of components that make up nearly a third of locally produced car content.
The reason South Africa has such a sophisticated and scaled automotive industry is part legacy, part incentive policy. When the country was an economic powerhouse in the 1960s, demand for passenger and commercial vehicles was so great that most brands happily established local manufacturing facilities.
As the economy diversified and the Rand depreciated throughout the 1990s, conditions became conducive to servicing export markets, which is what most local vehicle manufacturers pivoted to. And Government’s industrial policy regarding the automotive industry has been one of creeping localisation – a worthy idea, with some very unintended consequences.
Manufacturers must use a fixed percentage of domestic content to keep Government happy and retain the export credit incentives that make local vehicle assembly viable. And that percentage has been increasing, over time, to the current requirement of close to 40%, depending on specific formulations. The goal in future is to raise this to 60%. That means the domestic supplier base needs to grow to achieve that 60% number, but Eskom is making that nearly impossible.
It’s not just alternative power, it’s storage too
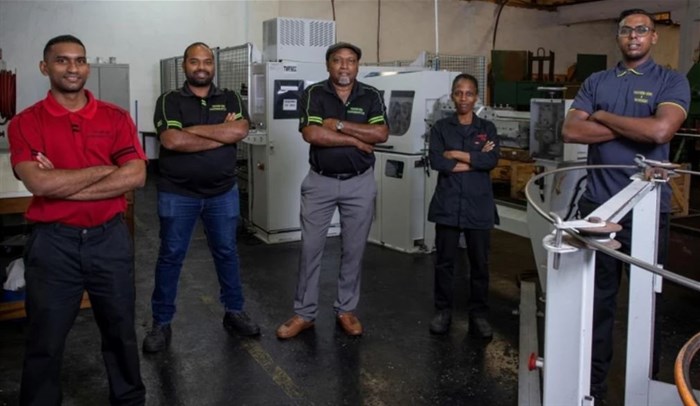
These are the true heroes of South Africa’s world-class auto industry, the small-scale suppliers.
It is a credit to the quality of local suppliers that luxury car buyers in many of the world’s wealthiest cities own cars of which about a 3rd is made up of South African engineering content.
But what happens when stage 6 load shedding keeps happening and smaller suppliers, without the shielding of alternative energy sources, start running way behind schedule – or simply go offline for weeks on end? Direct-feed solar is a huge benefit, but to run late shifts after sunset, battery capacity is required. And energy storage remains notably expensive, making it prohibitive for many small businesses.
There is, of course, a tremendous sense of irony in the fact that battery storage is so expensive, due to import tariffs. Broadly the same tariffs are making it so challenging to price electric vehicles competitively and stimulate local demand.
We have a real-world example of what will happen to South African vehicle assembly if a higher frequency of stage 6 – and higher – load shedding persists: there will be a lot of incomplete cars and unfulfilled global delivery commitments.
For the last year and a half, there’s been a global shortage of new vehicles due to one sub-type of componentry being difficult to source – the semiconductor (possibly the smallest and lightest part of a new car). The semiconductor crisis illustrated how vulnerable vehicle manufacturing could be due to an overreliance on external suppliers instead of vertical integration.
The semiconductor crisis proved how complex modern cars have become. There was no option to switch and substitute between suppliers and specifications with a component as sophisticated as a semiconductor.
And that theme applies on a very granular level across the South African domestic automotive supply chain. There just aren’t enough redundancy suppliers because of the just-in-time and just-in-place production systems that all car companies have copied from Toyota in preceding decades; those strategies are all about running ultra-lean/within very narrow margins.
Off-grid and running shifts

South African OEMs, such as FMCSA, have invested in solar. But how many small engineering businesses can do the same?
What is the nightmare scenario for South African automotive manufacturing? It’s the risk that skilled locally component suppliers might liquidate their business after a bout of prolonged power outages. All the best intentions and solar panels at OEM assembly facilities do nothing to protect suppliers from stage 6 and worse.
It’s credible and prudent that BMW, Ford, Isuzu, Nissan, Mercedes-Benz, VW and Toyota have journeyed to a position of relative independence from the disaster that is Eskom. But they remain deeply vulnerable to the risk of stage 6 and worse. Without specific locally sourced components, there will be no fully assembled vehicles rolling off their production lines and being shipped offshore, to earn those credits.
Supplier vulnerability was never a theme of discussion until the pandemic and the resulting semiconductor crisis proved exactly how exposed large car companies were to external influences. Solutions? During the deepest pandemic panic, there was an understanding that car companies would financially support select global suppliers. It was a matter of mutual survival instead of corporate generosity.
But the pandemic was always going to be temporary. Eskom’s power crisis, by contrast, has been a permanent feature of the South African economy for the past 15 years and, alarmingly, the situation shows no signs of improving.
Small business needs help

SA-built bakkies, travelling by road, for export by port. But will the volumes continue to grow, into the future?
The Department of Trade and Industry, which is mandated to grow the automotive industry, reduce risks to business and enhance entrenched employment diversity, is doing nothing. Small automotive industry suppliers need relatively little power, compared to large industrial users, but they need it consistently. If the government enacted the 100MW private generating laws, various build projects across urban industrial zones could solve the issue. But it hasn’t.
The talk is about South Africa’s automotive industry transforming in line with the motoring world’s transition from ICE to new-energy powertrains. That will require new production systems and local suppliers producing complex battery chemistry slurries, where power outages would be a total disaster.
When your CNC machine stops milling a metal part, that’s not great, but it can restart and complete the job when power is restored. But battery chemistry? All those solvents and sensitive coasting require meticulous processing and don’t take kindly to interruption.
What’s the worst-case scenario for the local motor industry? Instead of local sourcing and true “proudly South African built” vehicles, we could experience a future of many CKD kits, where you only fasten a few elementary parts, completing a vehicle which is effectively imported, in a state of near completion. In this dystopian future, South Africa will still have an automotive production sector, but it will be an artificial one, without the depth of skilled employment and career progression it has offered since the mid-2000s.
Then there is the impending end of the current generation of vehicles built locally. Each manufacturing plant has to bid for whatever product comes next and if our local plants don’t meet the standards of the German/Japanese bosses (due to constant delays caused by power shortages) they will simply shut up shop and go elsewhere.
Even worse would be the loss of a diverse and thriving small business sector of technical suppliers that keep the country in touch with global technology trends – one that offers true labour upskilling.
This article was originally published on Cars.co.za...