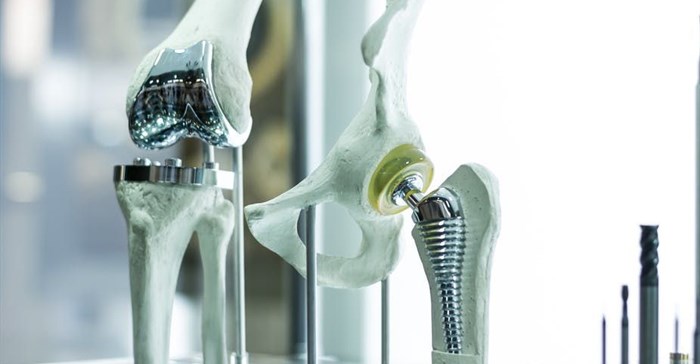
Low-cost alloys would pave the way for affordable medical implants and prosthetics. Monstar Studio/Shutterstock
Titanium has comparable strength to steel, the world’s most used metal, but is about 56% as dense and 45% lighter. Pure titanium is very difficult to extract from ilmenite and so it took about 145 years before the metal became generally useful.
Titanium alloys are made when controlled amounts of other elements – such as chromium, iron, vanadium, aluminium, nitrogen, niobium, molybdenum, ruthenium – are added to titanium.
Adding other elements to titanium can make it stronger or more resistant to corrosion. This, alongside other qualities, makes titanium alloys sought after in the aerospace, automotive, chemical, jewellery, biomedical, construction and other industries.
But titanium and its alloys are very expensive. Because titanium is difficult to extract from its ore, creating finished products involves many complex steps which demand a lot of energy and generate a lot of waste. For instance in the aerospace industry, where it is most commonly used, 11kg of titanium only makes 1kg of a finished product.
My colleagues and I are looking into how we can develop new low-cost titanium alloys in South Africa that could be used in non-aerospace sectors. Research like this is happening elsewhere in the world as scientists work to reduce the cost of titanium alloys.
If our work is successful, to my knowledge, these may be the first locally designed low-cost titanium alloys in South Africa. Low-cost alloys would pave the way for affordable fuel-efficient cars and affordable medical implants and prosthetics. The industry would also create job opportunities and generate revenue from sales.
Types of alloy
Titanium alloys can exist in three basic forms – alpha, beta and a combination of alpha and beta – depending on the amount and type of metal that is added.
Alpha titanium alloys are created when elements like aluminium, tin, oxygen and nitrogen are added to titanium. This allows the alloy to keep its structure in temperatures of up to 882°C and improves its strength. It’s also resistant to corrosion and creep – meaning it’s slow to deform over a long period of exposure to high levels of stress.
But alpha titanium alloys are more difficult to form into shapes and, compared to other alloys, don’t improve when heated or cooled. They are typically used for aerospace structures, engines and vessels that have to endure pressure.
Beta titanium alloys are made when large amounts of elements – like iron, vanadium, chromium and molybdenum – are added. The room temperature strength of this alloy is high, while its high temperature strength is poor. These alloys can easily be formed into shapes, even at room temperatures, making them an attractive material for orthopaedic implants.
The third type of alloy combines alpha and beta. This means considerable amounts of both alpha and beta stabilising elements – like iron and aluminium – are added. This gives the alloys a good combination of strength and ductility. They are by far the most developed and most utilised alloy. They are suitable for a wide range of applications from aerospace to automotive and biomedical industries.
Cheaper alloys
Our focus is on making a cheaper type of the third alloy: combination of alpha and beta.
We are doing this by changing the amounts of elements that are in the commercial alloy, known as Ti-6Al-4V. For instance, we replace most of the vanadium with iron, because vanadium is rare and expensive, about 150 times more expensive than iron. We have to be careful in our proportions because, for instance, iron could could segregate during melting and form different compounds.
We also reduced the amount of aluminium in the alloy. This is because previous studies reported that titanium alloys containing aluminium were difficult to form, and so resulted in the wear and tear of tools.
The next step was to reduce waste material when the alloys are being formed into shapes. Forming titanium alloys into different shapes usually accounts for 30% of the total cost of producing titanium products, and up to 20% waste generated.
To do this we looked at how far microstructures (internal structure than can only be seen with microscopes) can be manipulated to get the desired properties in the alloys. This would reduce the cost during commercial production because we know how far we can stretch or press the alloy without it breaking.
Producing alloys
We produced the alloys by a conventional technique called vacuum arc melting. The vacuum arc melting furnace is located at Mintek – South Africa’s national research and development organisation.
The limitation with this is that only button-sized samples were produced. So we could not make samples for a wide variety of tests.
We compared the hardness of the alloys and found that the newly-made alloys had higher hardness values compared to commercial alpha and beta alloys. In some cases they were comparable.
We also examined how the newly-made alloys corrode in salt and acid solutions and found they had better corrosion resistance in both solutions.
We were able to test samples of the alloys at different temperatures and forming speed to find the best combination for forming the alloys into shapes without defects. We saw that the alloys had a wide processing window. Only a small set of temperatures and deformation speeds had to be avoided.
More to be done
There’s more to be done. We couldn’t measure the room temperature strength of these alloys because we needed bigger samples.
We have also not studied the weldability of these alloys or how easy it is to machine cut them into different shapes and sizes. Machining of titanium alloys accounts for about 30%-40% of the total cost of making them.
Through the support of a postdoctoral fellowship programme of the African Academy of Sciences, we received funding to continue our studies on the newly developed alloys. We are now able to produce bigger samples using the vacuum induction melting furnace at the Council for Scientific and Industrial Research.
The major challenge when making bigger alloys is that we had to improvise. We used a vacuum melting furnace that is not designed for making new alloys. The correct furnace is available in South Africa, but needs repair.
However, our results so far are encouraging.
This article is republished from The Conversation under a Creative Commons license. Read the original article. 