Robots are critical for South Africa
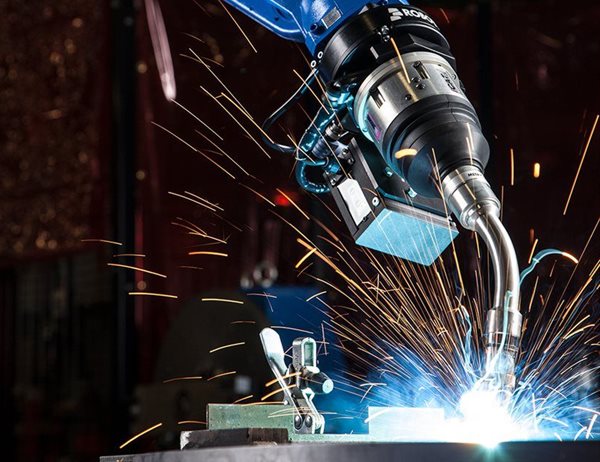
Due to the effects of Covid-19, many businesses might not have a choice but to rapidly adopt this technology – especially if they wish to survive in this new contactless society. Automation is no longer a subpoint in a five-year roadmap, but an item of critical importance.
Stringent health and safety measures have always been a massive concern for manufacturers, but many organisations will need to double their efforts to meet the new requirements in the post-Covid-19 world. Terry Rosenberg, chairperson of Yaskawa Southern Africa, says robotics in South Africa is already operating at international standards.
“Since our products come from an international source, they already adhere to the strictest health, safety and quality guidelines,” Rosenberg affirms. “As a result, we insist on the same standards in our operations. When a client purchases equipment from us, we recommend they take the mechanical and electrical safety facilities we offer as part of the robotic solution, to ensure safe and responsible machine usage. Further to this, we offer prescribed training for the safe functional use of the equipment once in the production environment.”
At the same time, Yaskawa is educating and preparing its clients to operate robots at the required global standards. “We have a special academy designed for end-user training,” Rosenberg explains. “This school provides modules on the basics of robotics, as well as the specific training for the application. Not only will the end-users learn how to use and program the equipment, but they’ll also be taught how to operate it in a safe environment. Furthermore, we provide ongoing training for new employees and other applications that might be introduced at a later stage.”
Robotic solutions
Globally, the automotive industry accounts for a significant portion of every robot produced. According to Statista, the automotive robotics market is the second-largest industrial robotics market. It’s no different in South Africa, where the sector is one of the largest users of robotics solutions. That being said, Rosenberg has seen the adoption of robotics in another key industry.
“We’ve seen growth in the food manufacturing industry, particularly in the material handling aspect of the production line where robots are used for the packing and palletising of large volumes of products,” Rosenberg says. “When there are mass quantities and heavy lifting, robots are capable of performing the functions that might be too dangerous or impossible for humans to execute.”
He adds that the food manufacturing industry is also cognizant of the impact of the 2017 listeriosis outbreak and now Covid-19. There’s a need to increase the cleanliness of operations and remove the need for human contact. And this can be achieved through the use of robotic solutions.
One of the most common misconceptions about robotics is that it’s strictly aimed at large enterprises; however, Rosenberg stresses this isn’t the case. In fact, he’s seen a substantial interest and increase in the usage of robots in the SMME sector in recent times.
“For some smaller companies, the only way they can produce the required quantity of products is through the use of robotics,” he explains. “As an example, we encountered a small company that operates its dispenser business from a farm. Due to the current pandemic, the demand for its automatic dispensers drastically increased. In order to meet the demand, the solution was to implement a robot that is able to work around the clock.”
While increasing its production, this business has also had to expand its labour force by 50%; therefore, creating more jobs. “There’s a fallacy that robots replace human workers,” Rosenberg says. “That isn’t the case at all, because we’ve seen robotic-powered industries turn into global giants that employ more people over the years. These organisations have been able to grow and add to their ranks thanks to technology. There will always be a need for people to complete challenging tasks that require human reasoning.”