Following the 2020 global Coronavirus pandemic, the ability to operate in a safe and clean working environment is one of the primary challenges in operations and maintenance. The post-Covid context is redefining what it means, exactly, to be "safe and clean."
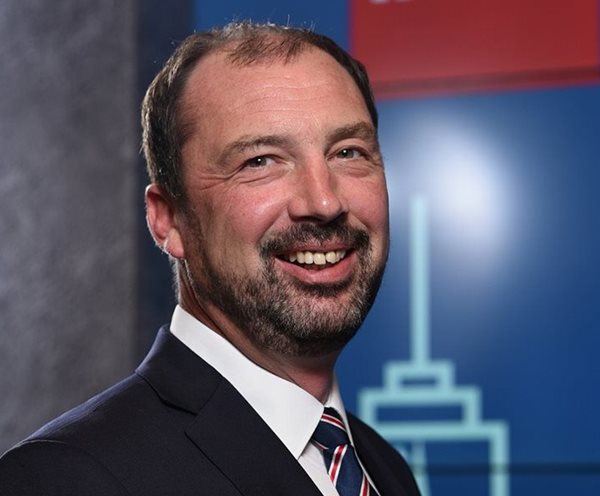
Phil Lewis, Infor VP Solution Consulting, EMEA
This new normal means organisations and businesses must evolve and adjust to meet increasing regulatory scrutiny and a heightened focus on clean practices.
However fluid the current situation and regardless of the existence or lack of official guidance, a successful enterprise should work to stay ahead of the curve, taking steps to prepare for whatever is next. This means embracing a new level of systemized asset management that continues to meet the highest standards of safety and cleanliness practices, analysis, and reporting.
There are – broadly speaking - five steps to ensure safe, clean operations: ensure continually clean practices by staff; update preventive maintenance schedules; identify assets at risk; be ready for changing expectations; and move from preventive to prescriptive.
To ensure continually clean practices by staff, creating and communicating clean operation protocols simply aren’t enough. Employees must put plans into practice. Anything less than 100% compliance is unsafe - and unacceptable. It is too easy to introduce a foreign contaminant into the operation, often unknowingly, compromising employee health and risking irreparable damage to organisational reputation. At the same time, regulatory agencies are issuing new guidelines on an almost-daily basis.
New rigorous practices
This new, intense level of required rigour will become part of new potential HR policies and there may even be a need to create education prerequisites for returning to the post-pandemic work environment.
The consistency of these practices will need to be addressed. Manual and paper record keeping are insufficient. Instead, automated maintenance checklists and workflows, alongside digitised staff scheduling, training, and manager signoffs will become commonplace.
End-to-end preventive maintenance (PM) processes will be critical in keeping environments both safe and clean. New maintenance schedules are likely to include a new set of work qualifications and operating conditions. PM cleaning procedures and approaches will change, with updated protocols for PM execution - especially the use of PPE and more frequent equipment cleaning.
When updating preventive maintenance schedules organisations can expect more tracking, monitoring, and analysis of any contamination incident, from questions about maintenance frequency to employee education and qualification. There are already new guidelines around flushing and heating systems, dictating more routine review of PM practices. This level of oversight will only increase across all industries. Organisations need to be ready with expanded documentation and records outlining their health and safety practices.
Identify critical assets
Identifying the most critical assets to maintain means having a sense of situational awareness around the primary physical resources that support safe and efficient business operations. For example, in a casino environment, the priority systems are air conditioning and ventilation. If those are not optimized, not only does revenue suffer but also, more critically, the property becomes at risk of contamination. In transportation, it’s all about the equipment that keeps people moving, safely and on time, which can call for something as fundamental as regular wheel inspections.
Under this new safe and clean mandate, identifying assets most at risk is critical. For example, prior to the pandemic, a transport risk assessment might focus on tyres, the heating and cooling system, and the engine. Post-COVID this expands to include areas such as the operator and passenger cabins. These assessments now must include when were they cleaned last, who cleaned them, and whether cleaning personnel were trained on new regulations.
The applies to all other facilities, from hotels to factories to offices: with new safe and clean operation protocol in place, are rooms or spaces being cleaned by people who know how to clean them according to new requirements, and can their action history be traced?
Aside from this softer look at critical systems, staff should convene around a trustworthy reliability ranking process. Tools that help determine the risk of assets as measured against specific criteria typically allow users to assign a Risk Assessment Index (RAI) and score to assets.
Adapt to new regulations
To be ready for changing expectations, maintenance organisations must continuously adapt to new health, safety, and environmental regulations. For example, consider the regulations changing facilities and asset management in a hospital before and after the pandemic. The change to HVAC systems or assets in surgery centres, emergency departments, and ITU?
Cross-industry governance will be augmented by industry-specific procedures. Regardless of the source these guidelines need to become the foundation, not the goal. The goal should always rise above and beyond the measures stated in external regulations.
This will necessitate more guidance, oversight, and perhaps unplanned visits from inspectors and auditors. As such, real-time reports and data on safety and cleaning adherence is imperative. Such reports should include procedures in place, implementation timelines and real-time reports of adherence, records of staff training or certifications, and details of hazardous materials and activities.
To move from preventive to prescriptive an asset management system that can adapt to a rapidly changing environment needs to integrate across facilities. It should include environmental controls, CAD, supply chain, and any other relevant systems. This enables access to rapid, quality, and accurate condition data.
A digitised system enables smart technologies that apply key analytics and can overlay the system with historical elements such as failure analysis, repair codes, warranty definitions, and original equipment manufacturer (OEM) expectations and strategies. This allows a shift from a preventive mindset to predictable and prescribed safe and clean practices.
Every organisation is eager to get back to work, but as various markets perform differently, more challenges are sure to emerge. Now is the time to focus on the processes, methods, and procedures that create a reliable, sustainable, and scalable asset management infrastructure, no matter what lies ahead.