Although underground mining is often considered more dangerous, this doesn't mean that surface mining is a 'walk in the park'. In fact, surface mining comes with its own set of unique safety hazards and can be just as dangerous when factoring in the risk of rockfall, high-wall collapses and continuous environment changes. Furthermore, surface mining is extremely labour-intensive and the more workers with heavy machinery required, the greater the risk of injury. In such a high-risk setting, hazard training is vital to create and maintain a safe working environment for surface miners in addition to meeting occupational and legislative compliance requirements. To this end, a certified training partner can help mining enterprises ensure that their workers have been adequately trained to understand, manage and respond to hazards encountered on a daily basis.
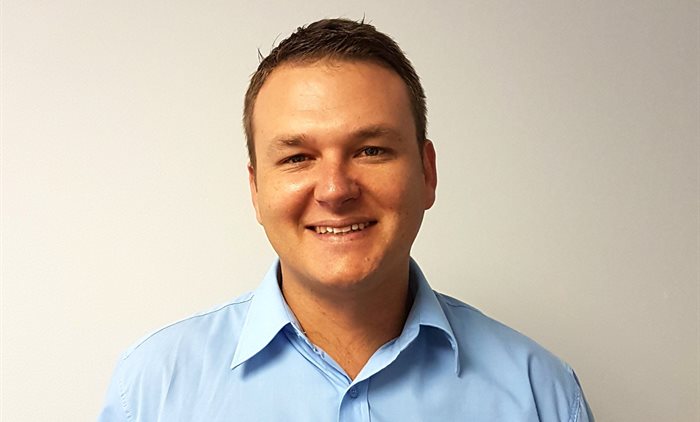
Jacques Farmer, MD at Prisma Training Solutions
The lowdown on surface mining
Making up a large proportion of all mining activities, surface mining is a method of extracting minerals that involves the removal of the terrain surface. This type of mining is used commonly to extract sand, gravel, stones, coal, iron and other necessary metals. Depending on the mineral extracted, there are five main types of surface mining, including strip mining, open-pit mining, mountaintop removal, dredging and highwall mining. Surface mining is the extraction method of choice for most mining companies, because removing the terrain surface to access the mineral load below is more cost-effective than tunnelling and drilling subterranean shafts to access mineral deposits underground.
Yashwin Bhoola, Christopher Mulindi and Goitseona Raseroka 16 Nov 2021 Fraught with hazards
While surface mining might be more cost-effective than underground mining, the risk of injury and fatality is just as high. Some hazards include cramped working conditions, entrapment, excessive noise exposure, inadequate ventilation and even unexpected explosive detonation. In highwall mining, hazards include equipment or roof fall, flooding, gas ignition, fire outbreak, rockfall, atmospheric deficiency and extreme weather conditions, including flooding and other fall hazards.
Safety starts with awareness
Inadequate safety competency means that if there is an accident, the injury is likely to be more severe with an increased possibility that the accident is fatal. Despite such an extensive list of hazards, surface mining can be safely conducted with the correct attention to safety legislation and proper training in safety equipment and protocols, such as the Mine Health & Safety Act. Although the goal of zero harm might seem lofty, it’s something that mining enterprises must strive for ceaselessly. With the proper training on surface mining hazards, workers gain understanding and awareness of their environment, which is the groundwork for preventing illness, injury and death in the workplace.
Minimising the risk of incidents and accidents in the workplace also minimises lost production time for the mine due to injuries and prevents workers from losing income due to their inability to perform as a result of injury. Striving toward zero incidents increases the likelihood of achieving production bonuses or health and safety bonuses, while contributing to a higher personnel morale - all thanks to a high standard of safety in the workplace. If that was insufficient incentive to pay closer attention to safety, there is always the looming threat of Section 54 of the Mine Health & Safety Act, which empowers a mine inspector to shut down operations where they have reason to believe that the health or safety of any person at the mine is in danger. With 68 fatalities in the mining industry in 2021 thus far, this is a marked increase from 51 in 2019, highlighting the urgent need to address safety deficits in mining operations.
Specialising in safety
An industry-certified and trusted training partner is essential for training workers on health and safety standards and how to maintain a safe working environment. When it comes to safety in mining, there can be no shortcuts, and mining enterprises shouldn’t implement health and safety policies without expert guidance in such a specialised and highly-regulated space. Employees must be equipped and trained according to their job specification, which includes being adequately equipped with the necessary knowledge, skills and attributes to be deemed safe and competent in their job.