Nando's chicken shortage: How the pandemic has made supply and demand tougher to predict
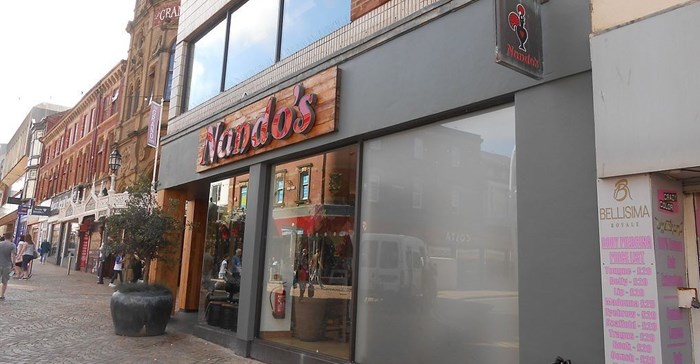
A chicken shortage has been blamed, and while reactions to the closures were satirised on social media, the problem is a serious challenge for the company.
Has anyone called 999 yet? �� https://t.co/FSeaPOIu4q
— Tim Bolton (@TimBolton01) August 18, 2021
Some blamed poor planning by retailers, but spikes of demand like this had not been seen before. And the pandemic continues to disrupt established supply chains.
A recent shortage of microchips for example is partly due to increased demand for appliances such as phones and games consoles, and a resurgence of coronavirus cases in Asia (where most microchips are made). The situation is so serious that Toyota is being forced to temporarily cut vehicle production by 40%.
Pandemics aside, patterns in demand for goods generally show fluctuations from day to day and from week to week. Some of these are explainable and predictable, for example, because of known periods of high demand, like Bank Holiday weekends.
Other changes defy explanation or prediction and are described in statistical forecasting models as “noise”. And although the nature of the next “noise disturbance” is not known, its impact can be measured and taken into account when setting stock levels. But even this careful approach breaks down when there is a sudden spike in demand, unlike anything that has previously occurred.
The current shortages of chicken at Nando’s are due to disruptions in supply, rather than demand, which could not necessarily have been expected.
From a forecasting perspective, sudden changes in supply are similar to sudden changes in demand. Inventory control systems usually base their stock calculations on a regular lead time (the length of time from placing an order to when the product arrives and is ready for the customer).
If there are occasional minor variations in the lead time, the calculations can be adjusted accordingly. But again, such an approach breaks down if there is a sudden major problem unlike any others that have gone before.
In this situation, we should have some sympathy for Nando’s. It would be incredibly wasteful of them to carry large stocks of raw chicken in anticipation of a possible major disruption.
Chicken out
If they were to do this in normal times, a significant proportion of meat would be unused and go off. Clearly, this is not a viable solution.
Instead, the problem of major disruptions calls for a different approach to forecasting, known as scenario planning. The problem at Nando’s seems to have been caused by labour shortages at their suppliers. And while the timing of labour shortages could not have been anticipated, their occurrence – at some point – could have been foreseen.
In a scenario planning exercise, managers imagine major causes of disruption that could happen in the future. This sort of exercise will never be perfect, and some events will remain uncovered, but this should not deter progress being made by thinking through potential supply chain problems and the company’s response.
For example, if an organisation is reliant on a single supplier for a product, then they may consider introducing a second supplier, who will also receive regular orders and can flex to respond to higher order volumes if there are problems at the first supplier.
This can also help to address responses to unexpected spikes in demand. And if a problem affects all suppliers, then plans can be put in place to order larger quantities of substitute products.
As a general rule though, the demand forecasting methods embedded in supply chain software should work well in normal times and can be used with confidence as the basis for stock replenishment planning. To anticipate extraordinary times, forecasting needs to shift from a system-based to a human-based activity.
Managers should attempt to foresee the major causes of shocks to their supply chains and put in place policies that will mitigate their effect. This will be beneficial not only to restaurant chains in developed economies, but also to humanitarian supply chains in which food, clothing and medicines are desperately needed.
This article is republished from The Conversation under a Creative Commons license. Read the original article.
Source: The Conversation Africa

The Conversation Africa is an independent source of news and views from the academic and research community. Its aim is to promote better understanding of current affairs and complex issues, and allow for a better quality of public discourse and conversation.
Go to: https://theconversation.com/africa