Enterprise Asset Management (EAM) has come a long way from the days of manual catalogues and vast spreadsheets detailing the inventory of an organisation. From the advent of barcodes to the ability to digitally catalogue, classify and search for assets, EAM is no longer the cumbersome task it once was.
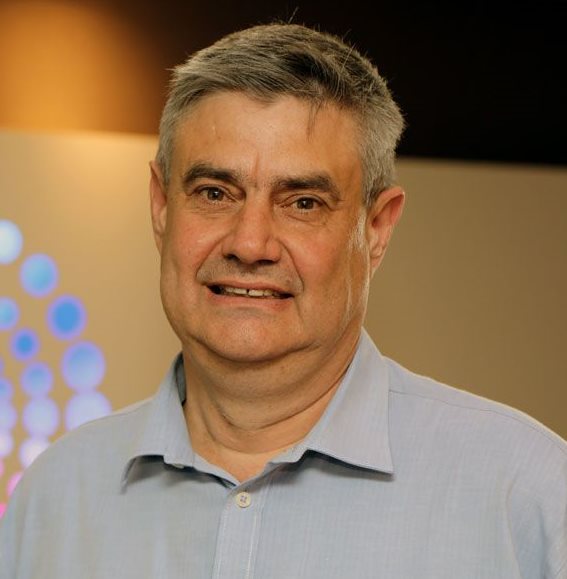
Stefan Jacobs, Applications Practice Head for Africa, Wipro Limited
The Internet of Things (IoT), however, has significant potential to transform EAM. With connected devices, all communicating on a network and sending potentially endless data, EAM can be transformed from just a cost centre to an area of competitive advantage. Real-time analytics of IoT data, enables proactive and predictive maintenance to become a reality, which can, in turn, result in reduced costs and strikingly enhanced customer service.
Traditional asset management typically involved spreadsheets full of information about assets, including serial numbers, date of purchase and so on. However, these manual systems were incredibly prone to human error, inaccurate at best, and subject to discontinuity, should the asset manager leave the organisation.
If anything went missing, an audit needed to be conducted, leading to additional expense of both time and money. Barcodes improved the situation significantly by enabling items to be digitally scanned and catalogued in a database.
Later, more effective search and cross-indexing capabilities were added, but there remained the issue of the database being managed by one person, who had to document everything on a spreadsheet.
Furthermore, it involved manually sticking a barcode label on each and every asset. In addition, all of this data was redundant without the ability to be analysed to provide any real value. Maintenance could be scheduled on a time or usage basis, but this was limited to certain types of equipment, and did not take into account any actual usage metrics.
The future
Fast forward to today, assets and devices are intelligent and connected, incorporating sensors that can transmit data continuously and the data can be analysed and managed without human intervention.
Connected devices offer a number of benefits, including better tracking and record maintenance, which vastly improves EAM. It is also possible to see exactly how long assets remain in use, whether they fail prematurely and so on, which helps businesses make better purchasing decisions.
However, the true value lies in the ability to conduct real-time analysis of the data being transmitted. Data on the state of a device can be used to determine when maintenance is required, if failure is likely, or whether there are any problems in operation.
This information can be used for predictive and proactive maintenance, which improves efficiency and reduces downtime and costs of repair. GPS chips can also be incorporated into devices for automatic scanning and tracking of the assets as and when it moves in and out of certain locations.
In addition, companies can utilise the data being sent by the devices they manufacture to gain insight and drive continuous improvements. Artificial Intelligence (AI) can augment and automate this process, with manufacturing machines automatically receiving the analysis and making adjustments.
Limitless potential
The potential here is practically limitless. For example, in the aircraft industry, a concept called ‘digital twinning’ has emerged, where sensors on aircraft components such as an engine are used to create a digital ‘twin’ of the device.
The digital model of the device creates a virtual image of the asset, enabling 24x7 monitoring, immediate identification of any potential problems, and expedient repair and proactive maintenance. This not only improves costs and maintenance, but it also enhances safety by a significant margin, ensuring that problems like engine failure can be more effectively prevented.
Connected devices and industrial IoT deliver automated processes, real-time data analysis, technology to quickly identify assets and components of equipment, as well as integration to management systems such as ERP.
This means that enterprise resource planning can finally become an end-to-end process. With real-time information available to enhance environmental management and accelerate business decision-making, organisations are empowered to manage losses more effectively, reduce productivity losses, missing assets, stock theft, improve billing processes and much more.
Companies that produce equipment can offer their suppliers and customers an integrated ecosystem for proactive maintenance and repairs, quality control and product improvements.
In the mining industry, maintenance can be scheduled to minimise the impact. Utility providers can sense potential failure in supply before breakages occur. Future developments could potentially include nanobots to inspect hostile environments such as sewers, as well as to conduct repairs without disrupting service.
With significant funding being spent on research and development to identify new opportunities for improvement, the IoT is set to revolutionise the way assets are managed. For businesses today, it can improve processes and turn a valueless necessity into a value-adding service, enabling predictive maintenance, improved customer service and enhanced asset management capability.