As part of its modernisation strategy, Anglo American Platinum's Tumela Mine has partnered blasting firm BME in an initiative to introduce emulsion explosives underground at its mine near Thabazimbi, Limpopo.
On 4 March, BME and Anglo American Platinum's Tumela mine announced the trial rollout of 54 portable charging units as well as the official opening of BME's training and maintenance facility on the mine - where some 180 underground personnel will be trained in the use of new equipment.
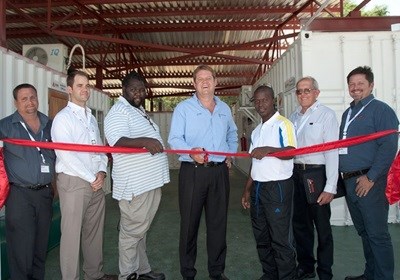
Official opening of BME’s training and maintenance facility at the Anglo American Platinum Tumela mine
"We aim to drill 12% fewer holes using this technology, saving us time at the rock face," said Tumela's Production Manager, Pierre Prinsloo. "Emulsion is safer to transport than traditional explosives as it only becomes classified as an explosive once it is in the blast hole. We also expect to use fewer explosives and transport cars underground, consume fewer drill steels, and have more flexibility with our shaft infrastructure."
The explosive characteristics of pump-able emulsions, and the improved transmission of energy to the rock mass surrounding the blast hole, lead to more efficient blasting - while being classified as UN Class 5.1 explosives makes them subject to fewer legal restrictions when being transported and stored.
Portable charging unit
A key element of the initiative is BME's portable charging unit (PCU), developed over the last seven years to take the benefits of emulsion explosives into the underground, narrow-reef environment. Improved safety and higher blast performance have made emulsions the dominant explosive medium in opencast mining.
"We have worked with Anglo American Platinum in testing this narrow-reef emulsion system for over a year," said BME's Senior Operations Manager, Selwyn Pearton, who has led the development of the PCU. "The success of our trials on Union, Tumela and Dishaba mines has now led to this roll-out of 54 PCUs across Tumela mine's underground operations."
Prinsloo said the testing process to date had included engagement with the union leadership, underground crews and employees in general, to ensure that all stakeholders were involved in playing a role in establishing the value of any new interventions undertaken by Tumela mine. He said the positive feedback and blasting results had led to this next phase.
"Our resources on site include a PCU workshop, a training centre and spares stores for the support of operations," said Albie Visser, BME's GM for South Africa. "We have 12 staff on site to ensure a smooth roll-out, including managers, administrators, maintenance technicians and training practitioners."
Among the breakthroughs achieved in the evolution of the PCU has been its compact, lightweight and robust design; weighing just 14kg, the pump component is carried separately from multiple 20kg emulsion bags. The sensitiser tank is also in a separate container - latched on to the pump just before charging - and renders the emulsion ready for blasting as it enters the blast hole.
Closed Emulsion System
"Our Closed Emulsion System prevents emulsion contamination and waste through the use of dedicated bag-filling stations, located underground close to the workface," said Pearton. "These stations are supplied from transfer cassettes, which bring the emulsion from our facilities on the surface."
He said the simplicity of the pump's design and operation procedures allows training to be conducted cost effectively and relatively quickly, with training facilities including a mock-up blasting rig to ensure real experience during training.
"The quality of BME's emulsion is another vital element of the process," said Pearton, "as it can be pumped numerous times without causing any product degradation; it can also be stored for extended periods with no reduction in quality."
To optimise efficiency and minimise downtime underground at Tumela mine, units can be easily 'exchanged' and replaced from the stores. Radio frequency identification (RFID) technology is employed to track the location of pumping units at all times.