The Covid-19 global pandemic has been a wake-up call for many industries, highlighting the incredible importance of digital transformation and adaptability, testing the capabilities of whether businesses can alter their practices almost overnight.
In these times of increasing instability and unpredictability, mining operations worldwide have had to grapple with the threat of total shutdowns or a reduced workforce, the likelihood of which continues to rise as the coronavirus spreads.
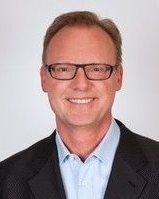
Doug Hanson, VP & General Manager & Digital Mine at Wabtec Corporation
What will be a major question going forward is how we use and engage with digital technologies, which have become intertwined with how many companies are dealing with the pandemic.
Entire labour forces are having to work virtually and embrace new technologies, while social distancing orders in certain countries means that remote monitoring of operations has never been more necessary.
For the mining sector in particular, those who have adopted digital mine technologies are already reaping the benefits, with tele-medicine for employees to help sustain their good health – and reduce potentially harmful exposure for healthcare workers – alongside remote monitoring and analytics that can sharply reduce potential economic loss.
In the current socio-medical climate, there are countries – such as Brazil – where mining has been declared an essential service, with operations continuing mostly as normal. However, take for example South Africa, where many mining companies have been forced to suspend operations entirely or work with skeleton staff following the recent announcement of a 21-day national lockdown.
Total shutdown scenarios
For those mining companies that are currently in total shutdown, the challenges arise when operations need to restart. However, this is where technologies such as Wabtec’s Digital Mine suite can
The Asset Performance Management (APM) toolset allows operators to monitor the health and performance of equipment as it restarts in a seamless way so that operations can resume as quickly as possible. Monitoring spikes in performance, blockages and lubrication requirements can also assist in preventing damage on start-up. From an operations performance management perspective, one can also look at how Wabtec, for example, can support our clients in streamlining the process, with advice on how we can remotely support the operation as production and processing resumes.
Reduced workforce and skeleton staff
Operators with a reduced workforce need as much support as possible to keep critical mining equipment functioning in an optimal way – particularly avoiding breakdowns, as the artisans and repairmen for such equipment are not easily able to travel under Covid-19 lockdown conditions.
Through the APM toolset, workers on-site can be supported through our remote monitoring centres stationed across the world, allowing non-stop monitoring of critical mining equipment.
Through the “Digital Twin” technology, a virtual copy of that equipment is created which can be remotely monitored. Using real time data coming through from the equipment, this can then be compared to the virtual twin. Through machine learning, abnormal behaviour patterns can be identified, meaning we can identify deviations, contact the relevant people in that limited workforce – and those not on-site – to alert them that something may be amiss. Then recommendations can be made as to whether action needs to be taken immediately, soon or if repairs can wait while we continue to monitor the health of that equipment.
During the Covid-19 period, we are already seeing real examples of how a very stretched on-site team can be guided on how to prioritise repairs and set down those critical maintenance periods.
The economic impact of Covid-19 and cost saving
Once operations do return to normal, it’s understandable that there will be scrutiny on costs, particularly the costs of maintenance windows for equipment repairs. Wabtec is focusing its efforts on how we can support our clients, and how our technology can be used to help optimise production uptime.
Importantly, predictive maintenance is key in preventing long repair periods. If a set of critical equipment needs to be operating to allow production to continue properly, one cannot have any of those essential pieces failing – or if they do, the shutdown period must be kept to a minimum. Following a determination of all the assets’ health and performance through our predictive analytics technology, one can decide on whether it’s necessary to shut down and during this window, if multiple pieces of equipment need to be repaired. This will help prevent a sequence of breakdowns. By maximising production, companies can try and reclaim the time lost during operational shutdowns. But the technology can also help by identifying when not to maintain.
While it may be considered good practice to replace a filter or set of bearings early, in such an unusual scenario where lockdowns can extend for weeks, sometimes it may be best to postpone certain minor, or unnecessary replacements to ensure operations can continue. By using APM technology, data analytics insights can stretch the use of the equipment and determine where maintenance is essential. These solutions can help improve productivity, reduce costs, while also maintaining safety.
Remote monitoring of employees during Covid-19
Operators using these technologies can also take advantage of in-place video surveillance data to monitor adherence to social distancing regulations and the presence of Personal Protective Equipment (PPE).
Thanks to key technologies coming from Stone Three, mine operators can use eCCTV cameras, to highlight areas where workers are congregating, where social distancing is not being adhered to, as well as locating high touch contact spots. A railing or a stairway leading to a machine that is constantly touched can then be flagged and attended to by the cleaning staff for sterilisation. Surveillance can also be used to determine if workers are using their PPE correctly, ensuring their face masks, eye protection and shields are in place.
Embracing new technology
As Covid-19 continues its spread globally, it’s likely we will see an uptake in these digital technologies in the mining sector. Operators have now been given an example of the value of digitisation if they have these technologies, and if they don’t they’ll be left wanting and looking to put them in place as soon as they can return to production.
As an organisation, Wabtec remains committed to assisting our customers in dealing with and responding to Covid, to keeping their critical operations safe and running as well as possible and leading the way to recovery once we’re able to get back to full production.