"Measure twice and cut once" is an old adage that every person who works with their hands has heard countless times, usually dispensed by their mentor as they learn the ins and outs of their craft. The learnings behind this phrase are to avoid having to duplicate your efforts, save time and eliminate any possibility of error in your results.
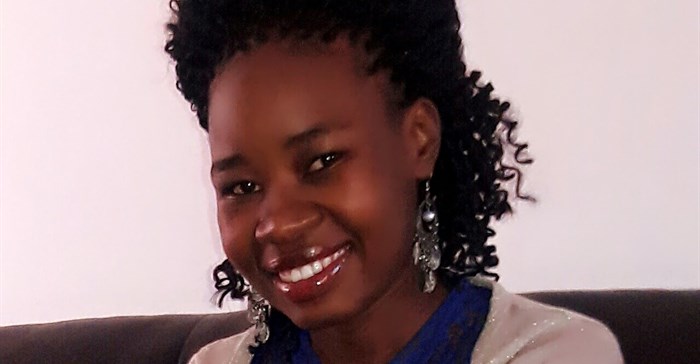
Manare Mokoatlo
In the world of mining operations – where every cubic millimetre of ore and every second of uptime counts – this is especially true. However, some operations are failing to meet their potential as a result of poorly drilled blastholes, which force them into duplicating blasts unnecessarily and ultimately hampering production in the long run.
Technical and geological factors
Blasthole surveying is a key part of blast planning and optimisation. These two processes are vital in ensuring that every blast goes off without a hitch, that the optimal amount and type of explosives are used and that the desired outcome is achieved.
When drilling blastholes, there are a number of technical and geological factors that can lead to an undesirable drilling pattern. From a technical aspect, excessive drilling and the use of worn out drill bits can lead to errors in blasthole structures. While rock types and ground water can cause drilling deviations, giving rise to poor blast results, low productivity, safety risks and environmental impacts.
Benefits of a well-planned blast
Blasthole surveying can identify drilling deviations as well as burden lengths and drilling depths. This is crucial to operations because a small burden length can mean too much rock being blasted from the bench face, while too long a length results in the explosive energy coming back up the blasthole.
A well-planned and successfully executed blast has several benefits. It can deliver operation-specific fragmentation levels, leading to improved productivity and removing the need for secondary blasts. This is because the correct level of fragmentation reduces the levels of loading and hauling, and optimises plant operations by making processes, such as crushing, more efficient.
A successful blast also enhances safety because it reduces the amount of flyrock, while its environmental benefits include meeting airblast and ground vibration limits.
While the information that surveying provides is crucial, it is what operations does with it that really counts. Through thorough measurement and analysis, operations can take corrective actions to reduce downtime and unnecessary secondary blasts, so mines can reap the financial and operational rewards.