Following injuries caused by unaddressed hazards on site and/or ineffectual personal protective equipment (PPE), 44 construction industry employees in the Western Cape were left with permanent disabilities last year, according to Deon Bester, occupational health and safety manager at the Master Builders Association of the Western Cape (MBAWC). He says that while this might not be a large number, even one disability is still one too many.
“I often observe employees using poor quality, inappropriate, damaged and ill-fitting PPE on sites. The normal rebuttal when questioning the situation is ‘well at least he is wearing PPE’,” says Bester.
He continues: “It is important to note, however, that employers must identify all hazards and risks that employees will be exposed to and put measures in place to eliminate or mitigate these, as per section 8 of the Occupational Health and Safety Act and section 9 of the Construction Regulations.”
Performing a risk assessment
Bester adds that section 2 of the General Safety Regulations further highlights the duty of the client to perform a risk assessment to identify hazards and to put control measures in place. “Only when all control measures have been put in place and the risk of injury still remains, then the appropriate PPE needs to be provided to the workers exposed to the risk of injury.”
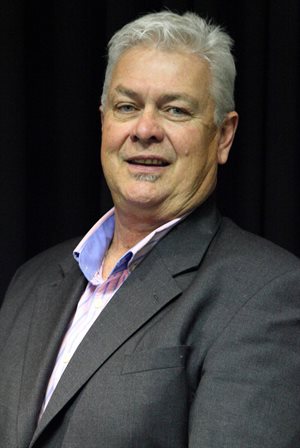
Deon Bester, occupational health and safety manager at the Master Builders Association of the Western Cape (MBAWC)
The occupational health and safety manager explains that the General Safety Regulations also contains guidelines regarding the type of PPE needed. However, the risk assessment done by a contractor will ultimately determine this. “We recommend that contractors do a thorough analysis of their PPE requirements and purchase the correct PPE from a reputable supplier. In fact, most PPE suppliers will be able to assist with performing a PPE needs analysis.”
“However, the biggest short-comings with respect to PPE is the lack of training of employees on the correct use and maintenance of PPE, coupled with insufficient monitoring of employees who are required to wear PPE on site,” adds Bester. “A lack of enforcement of the correct use of PPE is also a problem and could lead to injuries.”
Controlling hazards
Having said all of the above, we still do not appear to be controlling hazards, but throw PPE at every situation and hope and pray that this will work, points out Bester. “A classic example of this is so-called ‘working at heights’ or what the Construction Regulations refer to as ‘working from a fall risk position’. In this instance, the employer’s usual first port of call is to make workers wear full body harnesses, often with no safe place to hook the harness. Furthermore, in many cases, the height at which the person is working will not allow the shock-absorbing lanyard to properly deploy, resulting in the person hitting the ground.
“Bearing this in mind, section 10 of the Construction Regulations, which refers to fall protection, makes it very clear that fall prevention measures must be in place and only when these measures cannot be put in place do we revert to fall arrest. As such, any area that poses a risk of falling must be properly barricaded to prevent a person or objects from falling. This can be applied to all other tasks where we throw PPE at the situation instead of managing the risk posed to the workforce,” he says.
It is vital to note that there will always be situations where PPE needs to be worn, but incorrect, ill-fitting and poor- quality PPE will not help prevent an injury; in fact, it could contribute to an accident occurring and gives workers a false sense of security.
“We need to manage our risk on site and find ways to reduce the risk of injury by doing proper risk assessments and writing appropriate safe work procedures. Most importantly, we need to train our employees properly and enforce health and safety in the workplace,” concludes Bester.