VW SA produces its 2 millionth engine
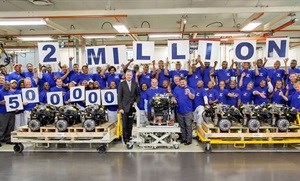
Locally, the engine is used in the South African top selling Polo and Polo Vivo which is produced at the Volkswagen manufacturing factory in Uitenhage, Eastern Cape.
The start of the EA111 engine production began in 2010 with the Engine Plant producing 89,000 engines. Since then, there has been a steady growth in production volumes with this year'' production set to reach the 175 000 mark.
"Of the 175,000 engines being produced this year, 77% is targeted for export to international markets," commented Richard Reid, head of Engine Plant at VWSA.
Volkswagen's international customers include manufacturing factories in China, India, Malaysia, Taiwan and Mexico.
"Last year in September, we introduced a fourth shift in the Engine Plant which increased the production capacity from 147,000 to 175,000 engines. The bolstering of production was due to the high demand from the Chinese market," explained Reid.
Over the years, new technology on the production line has been introduced to handle the increased growth in production. One of the new technologies is the state-of-the-art testing facility, which ensures that each engine is 100% proof tested before it leaves the line. Proof testing process includes leak, cold and electro-check testing. The cold test involves a dynamic test that turns the engine at 2000 rpm, conducting a vast array of measurements ensuring strict quality requirements are maintained.
This technology replaced the old Hot testing procedure, which involved every engine being taken off the line to separate testing facilities. The Hot test process was time consuming as it took nearly 15 minutes to test each engine. It was also costly as it involved testing the running of the engine with fuel and water.
Another development was the introduction of interactive technology on the line. The hi-tech interactive machinery assists the operators by guiding them with instructions via a screen which is connected to the electronic bolting equipment. The assembly line coupled with the latest technology block machining centres and highly trained employees ensures that the highest quality standards are maintained.
"All these improvements in Engine Plant have enabled us to produce an engine every two minutes. The introduction of the new technology and enhancement of our production processes has ensured that we are continually improve our products for both the local and international markets," said David Powels, VWSA Managing Director.