The construction sector is one of the least digitised industries in South Africa and globally. While this is largely attributed to the complexity of the industry, the power of data can no longer be ignored. It is at the heart of everything and if properly harnessed, can fundamentally change productivity in the industry.
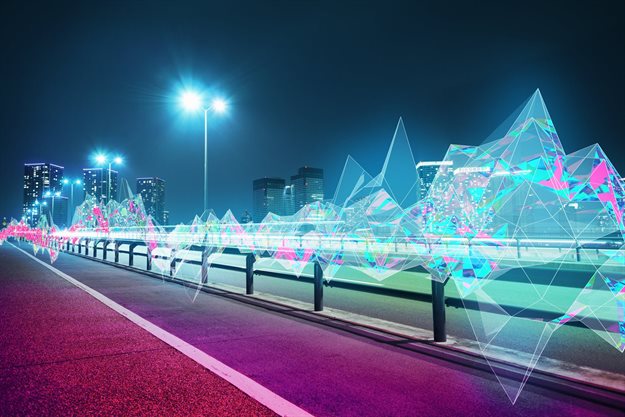
Image source: Gallo/Getty
Digital adoption in construction has been low, with the industry spending, on average, between 1-1.5% of turnover on information technology (IT) compared to about 3% across all industries, and between 5-10% for more sophisticated industries, such as banking.
Highly complex industry
There are various reasons for this. Firstly, construction is a highly complex industry with several stakeholders involved in the various projects. Collaboration amongst the stakeholders, from the client and main contractor, to all the sub-contractors, can be complicated. Secondly, it’s a project-by-project business and stakeholders and business processes differ from one project to the next.
The digital status quo of the industry does, however, need to adapt or it will be left behind in a fast-evolving world where collaboration, transparency and digital innovation are driving change.
As a first step, construction companies need to digitise their core business processes. Investing in the right software will help them run their businesses more effectively.
Real-time information
The solutions they choose need to provide real-time information to help them make informed decisions in areas such as estimating, project control, cost and enterprise management. This will help them improve controls, compliance, efficiencies and contribute positively to the bottom line for each project.
Research by the McKinsey Global Institute research shows that digitisation of the engineering and construction industry can lead to productivity gains of as much as 14-15% and cost reductions of between 4-6%.
The adoption of digital advances such as wearables and various internet of things (IoT) enhancements can also make a significant difference for construction companies.
Drones can be used for pre-construction site surveys, as well as during construction to check progress during the build. Wearables, such as virtual reality (VR) glasses, can be used to visualise the designs of the structure while under construction. In addition, computer vision technology (CVT) can be used to track external progress on construction sites, as well as to alert foremen or site agents to unsafe work behaviour or safety hazards on site.
One of greatest issues in the construction industry is the commencement of construction before the design is finalised and the true construction programme has been determined to the nth degree. This often has time and cost implications when changes in design or the construction programme lead to escalation.
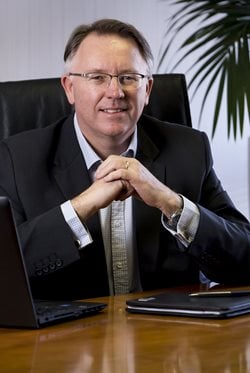
Andrew Skudder, CEO of Construction Computer Software
5D building information modelling
Here, the harnessing of 5D building information modelling (BIM) is critical. It helps establish how long a project will take and how much it will cost at each phase, depending on different designs, methods, building materials and fittings. The more work that is concluded up front to simulate the construction and iron out all the issues, the smoother the real construction will be.
And then there is equipment management – the ability to track where equipment is on site – using RFID tags and other IoT sensors. With the large number of tools and scaffolding commonly found on building sites, it is easy to lose track of equipment.
The importance of using technology to track resources, labour, equipment and material utilisation on site cannot be underestimated as it helps generate data that can be used to identify trends, inform decisions and enhance productivity on existing and future projects.
Often, companies don’t rebase their projects in terms of the resources they allocate to projects or the time it is going to take. For example, if trucks are standing still for much longer than they should be, a decision can be made to use fewer trucks or to schedule trucks to be on site at the right time.
Preventing slippage, cost overruns
Access to this type of information helps construction companies not only to make decisions about what resources to place on projects in future, but also in real-time. If data suggests a project is on time and under budget, then resources can be shifted elsewhere. More often than not, projects are over budget and over time. With access to the right data, construction companies can determine when they are over budget and devise strategies to amend the situation or prevent further slippage and cost overruns.
Ultimately, all construction technologies need to be integrated via a vertical cloud platform. This will see all data being fed into one place, whether through traditional ERP-type solutions, project control solutions, artificial intelligence or the IoT.
Enhancing productivity
In South Africa, where unemployment is high, digitisation and AI are often regarded with suspicion. Rather than resulting in job losses, these technologies have the potential to enhance productivity and cut out mundane tasks for key roles in the construction industry. It’s about modifying work rather than displacing jobs.
Instead of chasing down quotes from three different suppliers and conducting a manual comparison of costs and quality, estimators can use software to do the job faster and more efficiently. By removing the grunt-work from estimators, they are able to spend more time finding solutions to strategic issues relating to a project.
Ultimately, the ability to take data from conception through to operation really is where a fundamental change needs to occur in the construction industry. This will enhance productivity at every stage of the construction process.